Before our products reach stores, many hands have been involved in producing them. The textile industry is labor-intensive supply chain, spanning countries, cultures, and diverse communities. While we don’t own the companies we partner with, we are fully committed to ensuring workplaces that prioritize safety, respect, and equal treatment. We’ll explain how on this page.
Targets
All our suppliers in the first and the second tier* fully comply with our human rights standards and the national wage standards.
*In the fashion industry, tier 1 handles final product assembly, tier 2 processes materials (like dyeing or printing), and tier 3 supplies raw materials (like cotton or wool).
We’ve set up the Corrective Action Plans system, which helps identify and fix risks at the factories we work with.
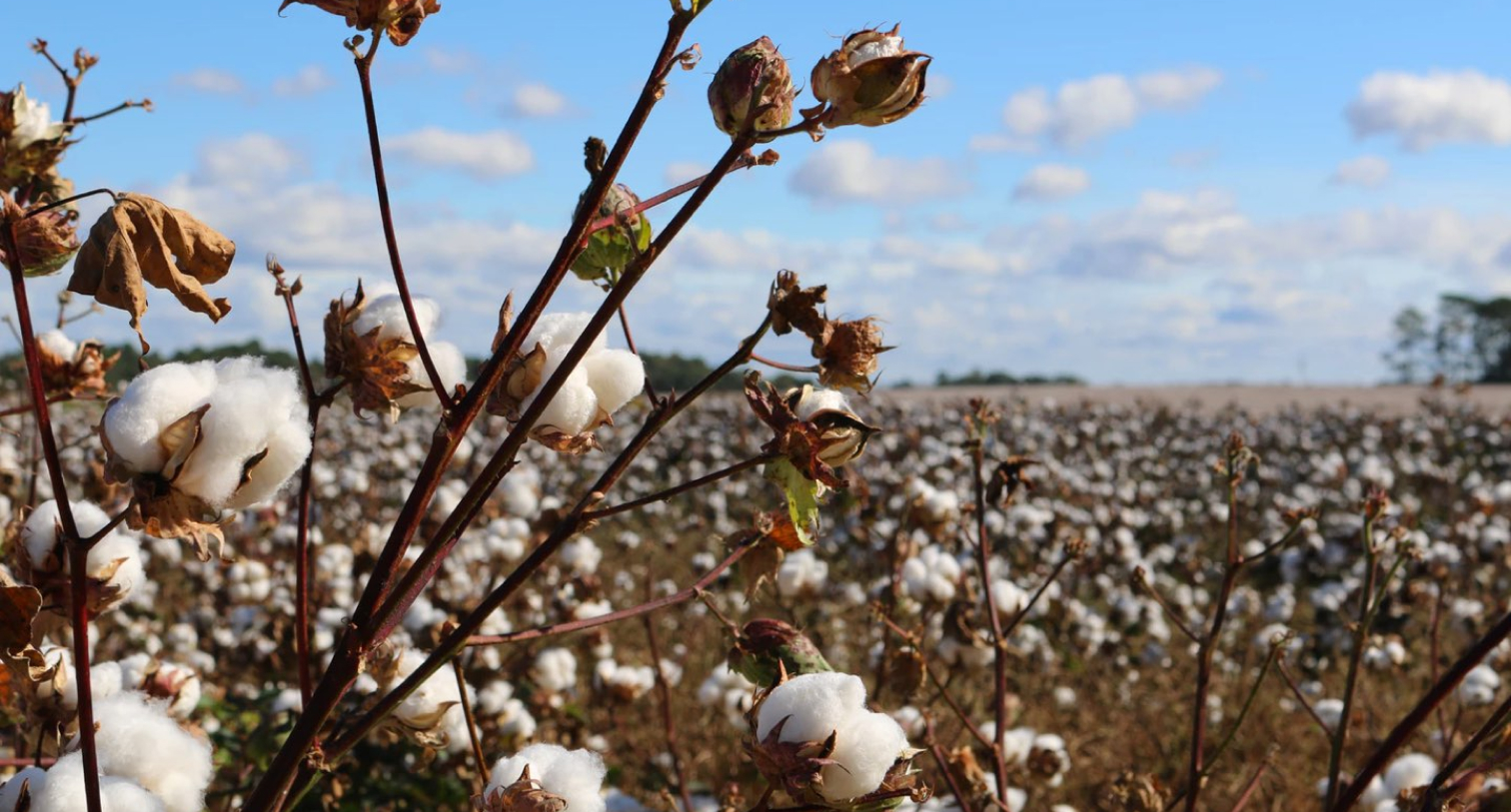
Code of conduct
A code of conduct is a set of rules and guidelines that explains how organisations should act in a responsible and ethical way.
It sets standards for behaviour that strives for fairness (like collective bargaining, gender equality and freedom of association), safety, and respect. At Just Brands, we follow the code of conduct set up by the AMFORI Business Social Compliance Initiative (AMFORI BSCI). This code of conduct is based on international labor standards as established by the International Labour Organisation (ILO), the United Nations (UN) and the Organisation for Economic Co-operation and Development (OECD). It contains 11 fundamental labor rights that we implement step-by-step, together with our partners. Before we partner with a new manufacturer, they must sign this Conduct of Conduct as well. AMFORI also provides workshops for manufacturers, and we encourage them to participate.
Download the code of conductCode of conduct
A code of conduct is a set of rules and guidelines that explains how organisations should act in a responsible and ethical way.
It sets standards for behaviour that strives for fairness (like collective bargaining, gender equality and freedom of association), safety, and respect. At Just Brands, we follow the code of conduct set up by the AMFORI Business Social Compliance Initiative (AMFORI BSCI). This code of conduct is based on international labor standards as established by the International Labour Organisation (ILO), the United Nations (UN) and the Organisation for Economic Co-operation and Development (OECD). It contains 11 fundamental labor rights that we implement step-by-step, together with our partners. Before we partner with a new manufacturer, they must sign this Conduct of Conduct as well. AMFORI also provides workshops for manufacturers, and we encourage them to participate.
Download the code of conduct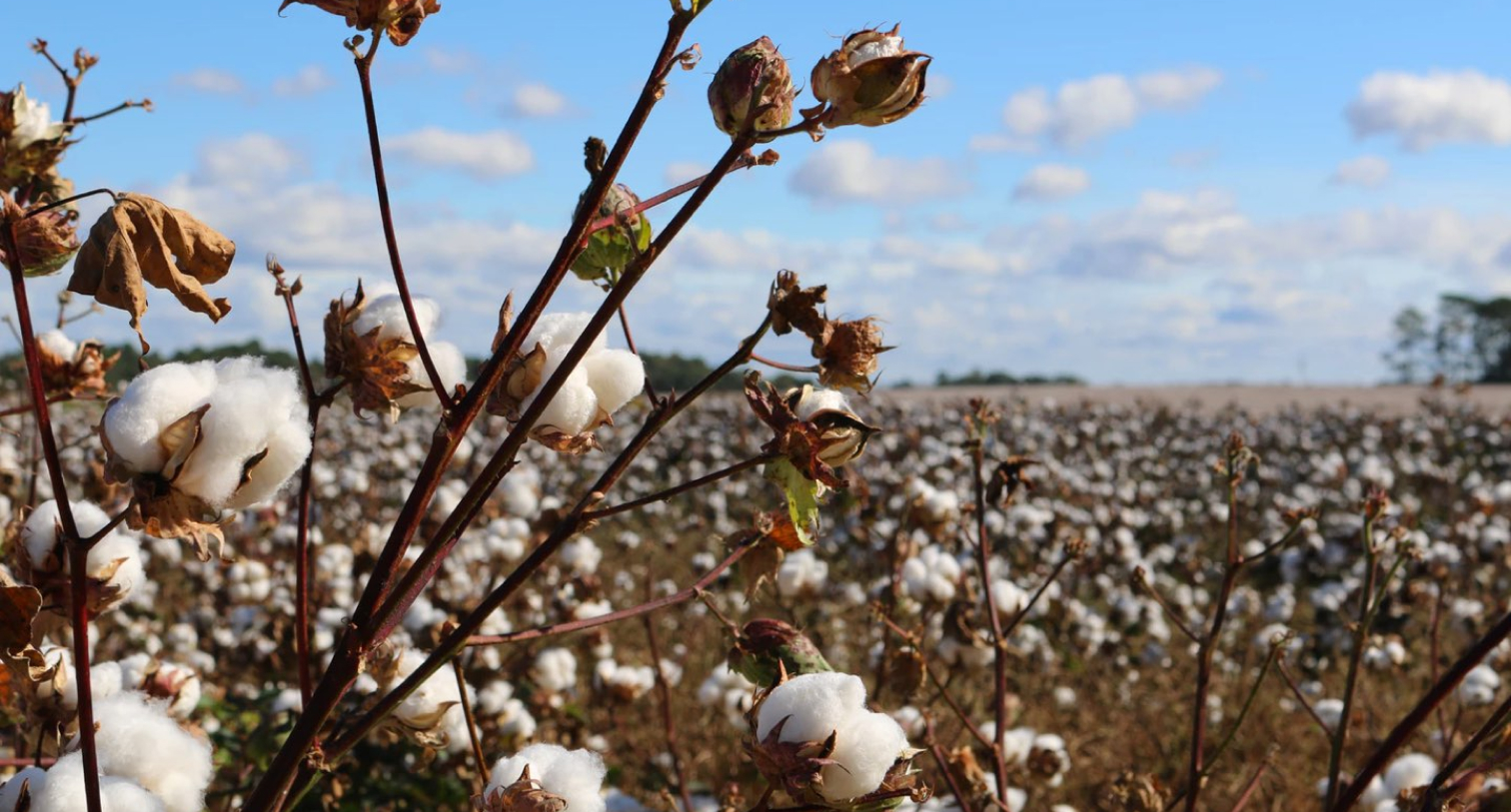
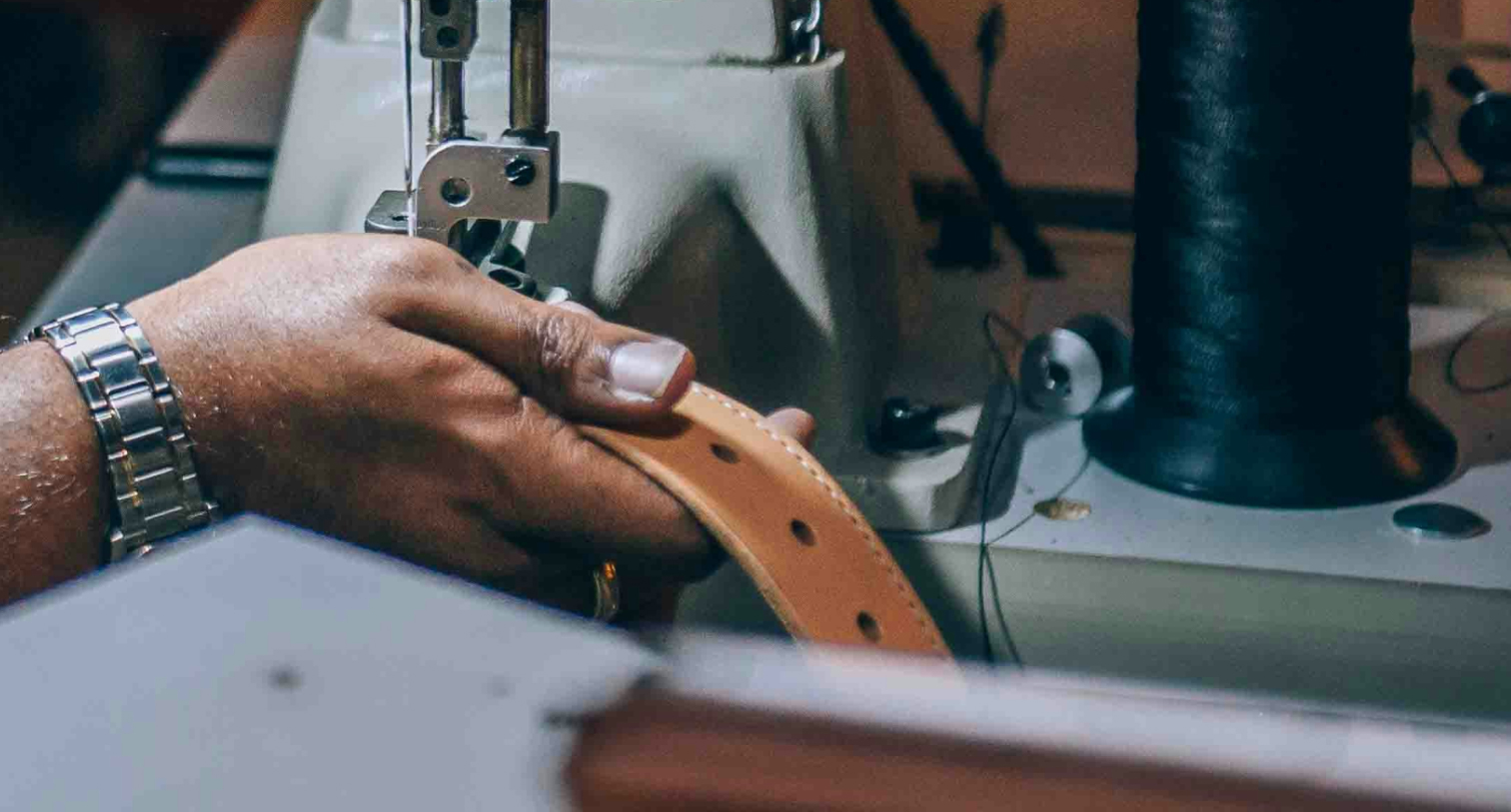
Independent factory checks
All factories we work with, have agreed with our rules and guidelines on how to act in a responsible and ethical way (our code of conduct).
Independent factory checks
All factories we work with, have agreed with our rules and guidelines on how to act in a responsible and ethical way (our code of conduct).
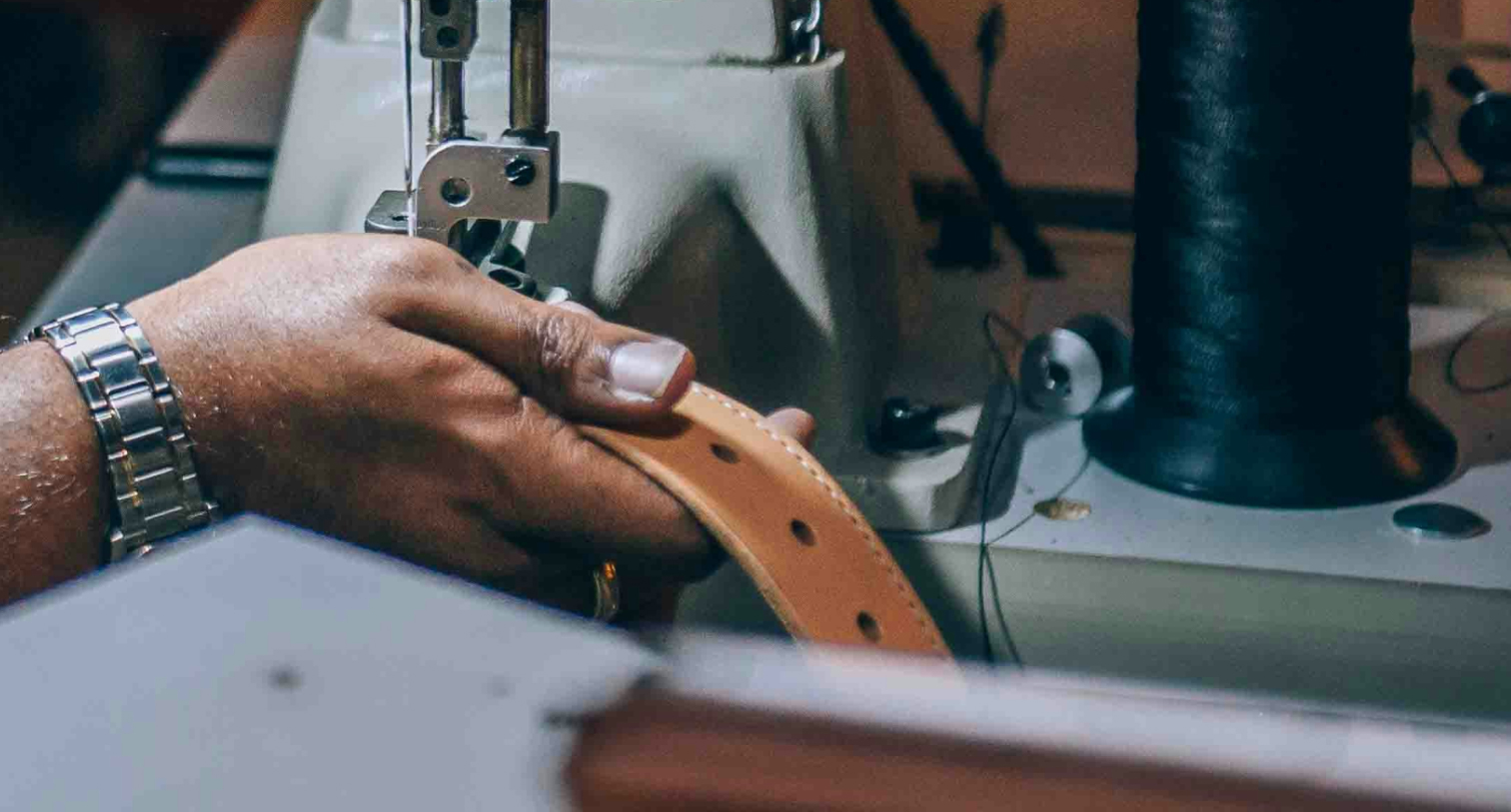
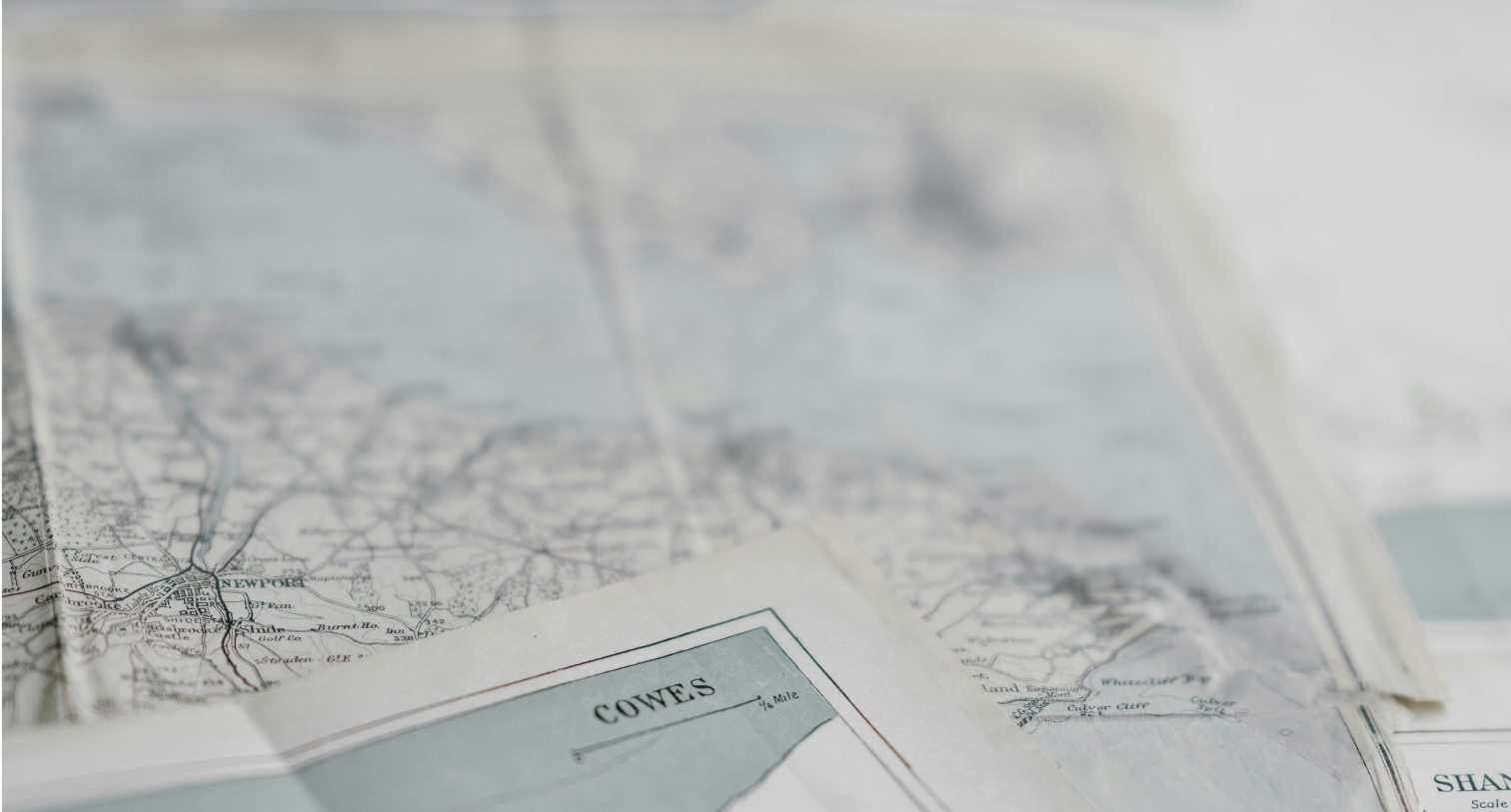
Risk analysis
In an international chain like ours, it is essential to be aware of the possible social risks involved.
We actively research risks like unsafe working conditions and unfair wages in our entire production chains and operations. We monitor working conditions by taking a clear, step-by-step approach. We start by identifying risks at the country and regional levels. Then we look closely at the conditions at our manufacturers. We review audit reports, talk directly with our manufacturers, and work with local stakeholders to quickly find and fix any issues.
Risk analysis
In an international chain like ours, it is essential to be aware of the possible social risks involved.
We actively research risks like unsafe working conditions and unfair wages in our entire production chains and operations. We monitor working conditions by taking a clear, step-by-step approach. We start by identifying risks at the country and regional levels. Then we look closely at the conditions at our manufacturers. We review audit reports, talk directly with our manufacturers, and work with local stakeholders to quickly find and fix any issues.
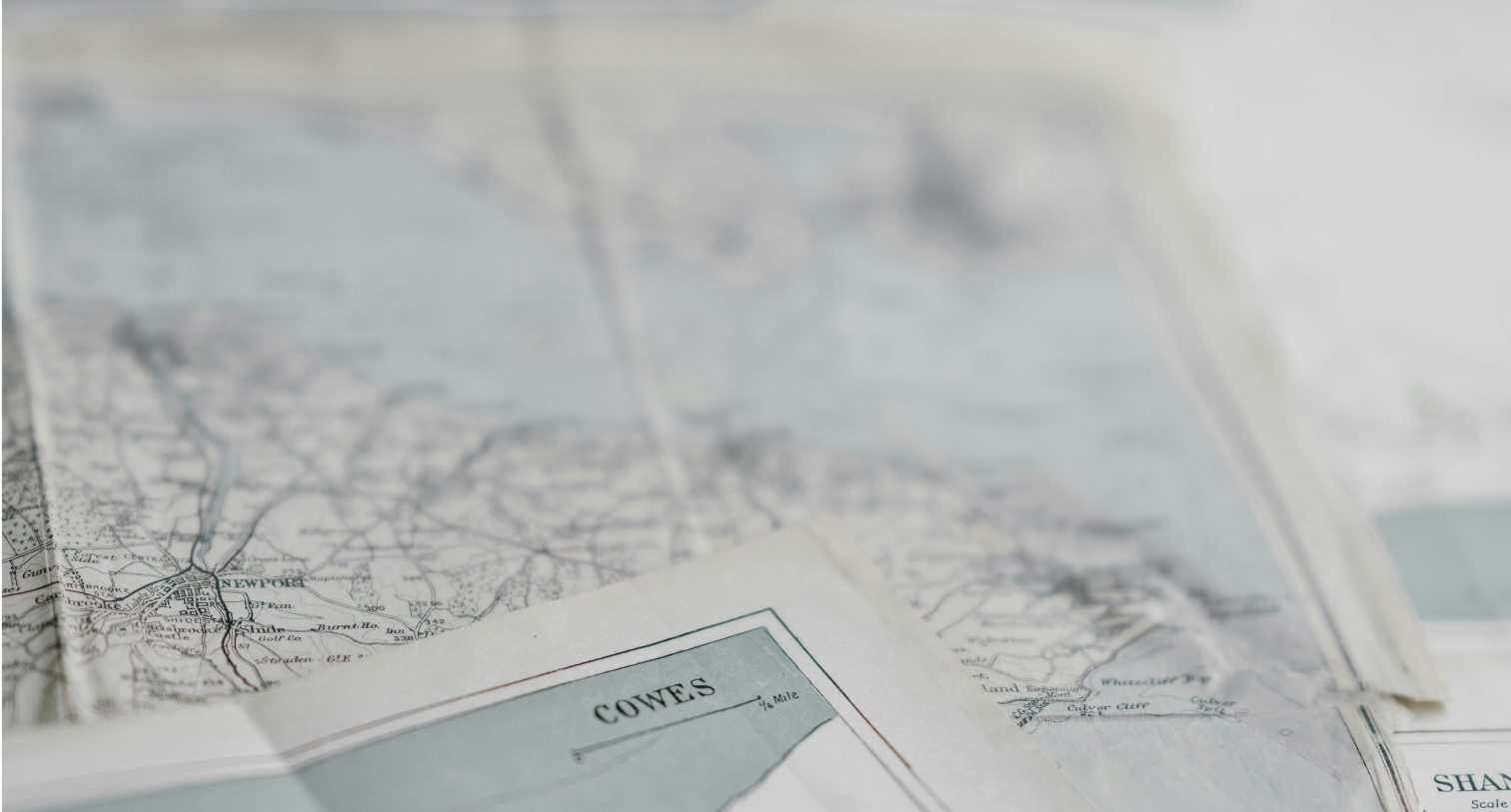
TRANSPARENCY
At Just Brands, transparency is a core value. We believe it’s essential for everyone— from manufacturers to customers—to clearly understand our stance on sustainability and the actions we’re taking. We also ask all our garment manufacturers across the globe to be transparent. Our manufacturers are free to choose their print houses, dye houses, and laundries—as long as they share all details. Once we purchase our collections, they must register the addresses of these partners. This keeps our production chain clear and helps us quickly address risks or developments in those areas.
Moreover, we take transparency to the next level by openly sharing all the garment factories we partner with on our supplier map.
View supplier map